Liquefied gas dehydration units
The liquefied hydrocarbon dehydration unit is designed to remove water from the liquefied gas stream to a level of 0.0001% (mass) or 0.02 kg/h. Liquefied gas dehydration is made alternately according to a given cyclogram in two absorbers. The parameters of the inlet and outlet flow of liquefied gas for the LPG drying unit are provided by the customer and are individual for each project.
Dehydration unit operation process:
The adsorber is designed for deep drying of LPG and is a vertical cylindrical apparatus, which consists of a cylindrical body with two elliptical bottoms and internal devices.
The design of the adsorber provides hatches for loading and unloading the adsorbent into the adsorber.
The adsorber is equipped with all necessary instrumentation, sensors and actuators
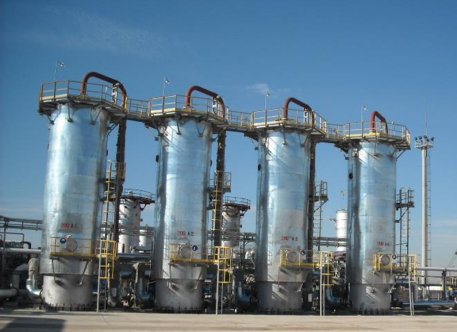
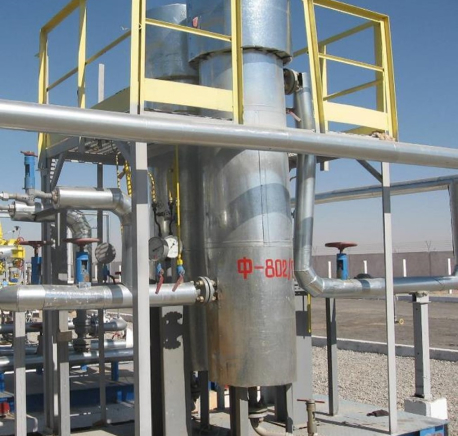
The dried LPG filter is designed for cleaning the liquefied gas from the adsorbent dust. The filter is a vertical cylindrical apparatus which consists of a cylindrical body.
An elliptic bottom is welded to the bottom part of the body and a manhole with a flange connection is installed in the upper part to enable installation and replacement of the filter elements. The filter body is all-welded.
The design of the filter has a fitting for draining the liquid from the unit in the lower part. The filter is equipped with a pressure gauge and a differential pressure gauge on the filter elements.
The heat exchanger is a horizontal shell-and-tube apparatus with U-shaped heat exchange tubes located at the vertices of the triangles, two-pass through the tube space, mounted on saddle supports. The heat exchanger is equipped with a number of process connections.
The apparatus is designed, manufactured and tested in accordance with the specifications of the supplier’s plant and the requirements of the Federal norms and rules in the field of industrial safety Industrial Safety Rules for Hazardous Production Facilities Using Overpressure Equipment.
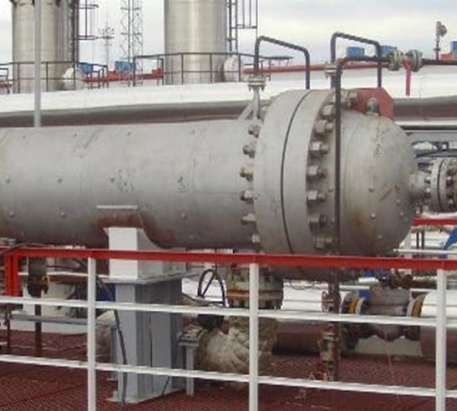
When choosing the material design of the equipment, it is taken into account:
- operating and design conditions;
- composition and nature of the medium (corrosive, explosive, toxic, etc.);
- technological properties and corrosion resistance of materials to ensure the design life.
For example, the parameters of the input and output flow of liquefied gas and the composition of the input and output flow for the LPG drying unit (parameters are individual for each project):
Liquefied Gas Stream |
LPG for drying |
LPG after drying |
---|---|---|
Operating temperature (°С) |
40 | 40 |
Operating pressure (MPa (g)) |
1,8 | 1,7 |
Molecular weight (kg/kmol) |
51,43 | 51,58 |
Molar consumption (kmol/h) |
328,62 | 327,39 |
Mass flow (kg/h) |
16901,00 | 16883,91 |
Volume flow (m3/h) |
31,17 | 31,15 |
Density (kg/m3) |
516,9 | 516,4 |
Heat capacity (kJ/kg °С) |
2,68 | 2,69 |
Dynamic viscosity (cP) |
0,114 | 0,112 |
Thermal conductivity (W/(m K)) |
0,64 | 0,17 |
Surface tension (dyn/cm) |
5,08 | 5,08 |
Stream composition |
Inlet |
Outlet |
---|---|---|
Water | 0,032 | 0,0001 |
Hydrogen |
0,003 | 0,003 |
Ethane |
3,430 | 3,431 |
Propane |
28,315 | 28,324 |
Isobutane |
21,546 | 21,553 |
Butane |
45,489 | 45,489 |
Pentane |
0,284 | 0,284 |
Isopentane |
0,520 | 0,520 |
Hexane |
0,103 | 0,103 |
Ethylene |
0,027 | 0,028 |
Propylene |
0,041 | 0,041 |
Our advantages
Own calculation for each
unit of equipment
Application of any type of adsorbent based
on customer requirements (imported/Russian)
Selection of equipment based on
customer requirements (imported/Russian)
We guarantee the final result, as well as for each separate technological unit of this installation